The evolution from lighting to service
An Interreg Europe - Design4innovation case
Mid 2016, ETAP Lighting started developing its LAAS (light as a service) concept. In 2017 efforts were continued in the APBC program ‘CONNECTING THE DOTS’ that brought together product designers and producing companies.
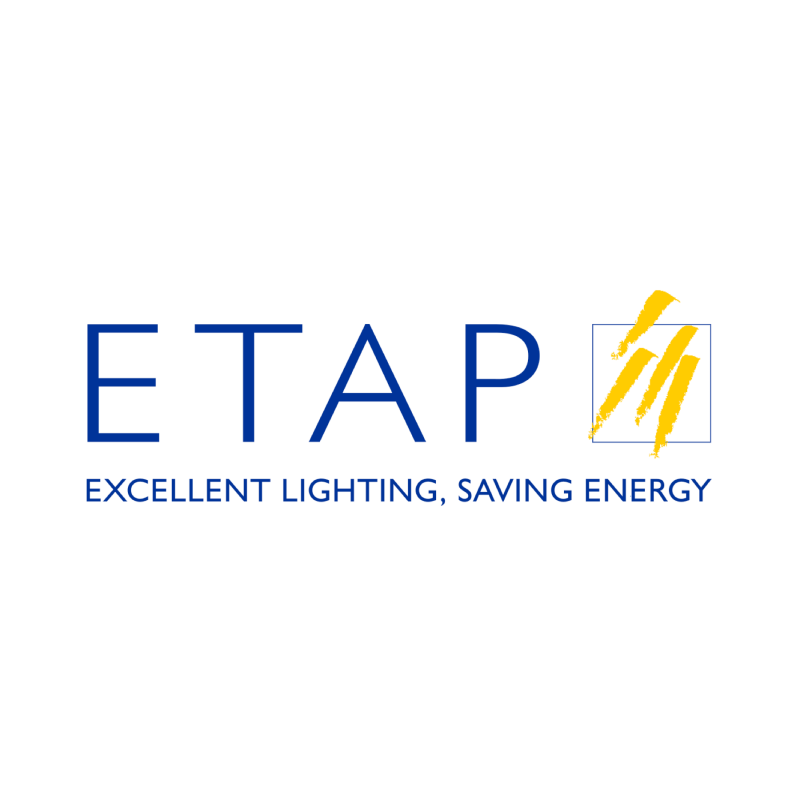
What was the challenge?
ETAP Lighting is an independent European company, founded in Antwerp in 1949. They are active in professional interior lighting for offices, factories, schools, hospitals, shops and hotels.
ETAP develops lighting solutions from A to Z: they create lighting concepts, design, industrialize and produce lighting fixtures, provide advice and make lighting studies, supply the luminaires and provide an after-sales service. Because they follow the process themselves, they can guarantee the highest quality at every stage.
By constantly innovating, they have acquired a leading position in the European lighting market. Each year, ETAP invests 6 to 7% of their turnover in research and development. ETAP has local teams of lighting specialists in eleven countries. About 500 people work for ETAP across these countries.
How did design help?
ETAP has developed its LAAS (light as a service) concept starting mid 2016 in a workshop managed by Dutch CIRCO and the technical university of Delft. Efforts were continued early 2017 in a program of APBC (Antwerp. Powered by Creatives.), called ‘Connecting the dots’ that brought together product designers and producing companies. Product designer Stefan Schöning was ETAP’s obvious choice.
The basic idea is that ETAP provides the lighting of a building as a service for an agreed period. ETAP takes care of everything: the lighting design, the production of the luminaires, the installation, the tuning of the lighting to reduce energy consumption, the maintenance of the equipment, and finally its dismantling to make it ready for its next job.
The customer doesn’t need to make any capital investments. State of the art LED lighting is provided for a fixed annual cost that even includes all the maintenance. In many cases, the total operational cost is lower than the operational cost of the old lighting equipment.
For ETAP, servitization is a strategic choice for customer intimacy. Moreover, since ETAP remains the owner of the lighting equipment, it is in pole position to provide a circular destination at the end of the contract period.

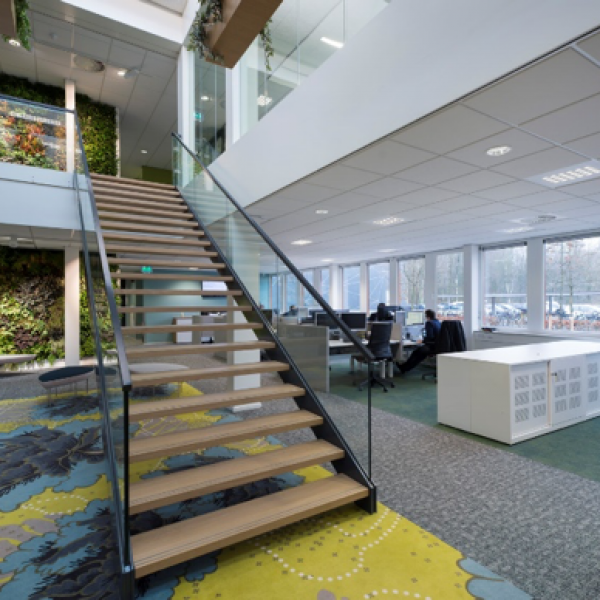
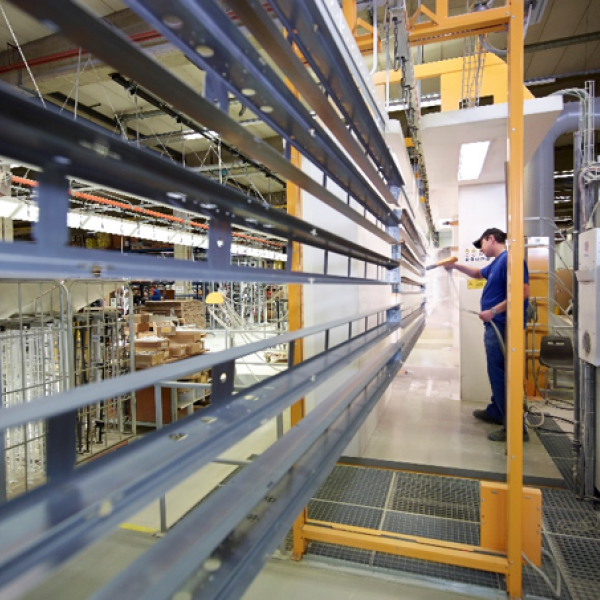
What is the impact?
ETAP products have been designed for a long lifetime and a high lumen maintenance factor, a prerequisite for a service arrangement. Recent LED products were designed in cooperation with product designer Stefan Schöning, who also assisted ETAP for the design of its new business model.
ETAP expects a boost of lighting renovation to be made possible by its LAAS concept. It estimates that in the next 5 years a total building surface of about 750.000 m² will benefit from renovated lighting thanks to this concept. The specific power will be reduced from about 2,5W/m²/100lx to less than 1W/m²/100lx, leading to a total energy saving of over 14 million kWh per year, a CO2 reduction of over 750 ton. Production and servicing of these lighting installations will create extra jobs, as well in the central production facilities in Malle (Belgium) as in local sales hubs in the Netherlands, France and Germany.
ETAP wants to go far beyond energy saving and move further in design for circular economy, striving for easy servicing and repair, easy refurbishing and remanufacturing, total recyclability. Remote monitoring and tuning of the lighting to further reduce energy consumption is another important field of development. These efforts will drive the development program of ETAP. More than 30 people are involved in the product development activities of ETAP.
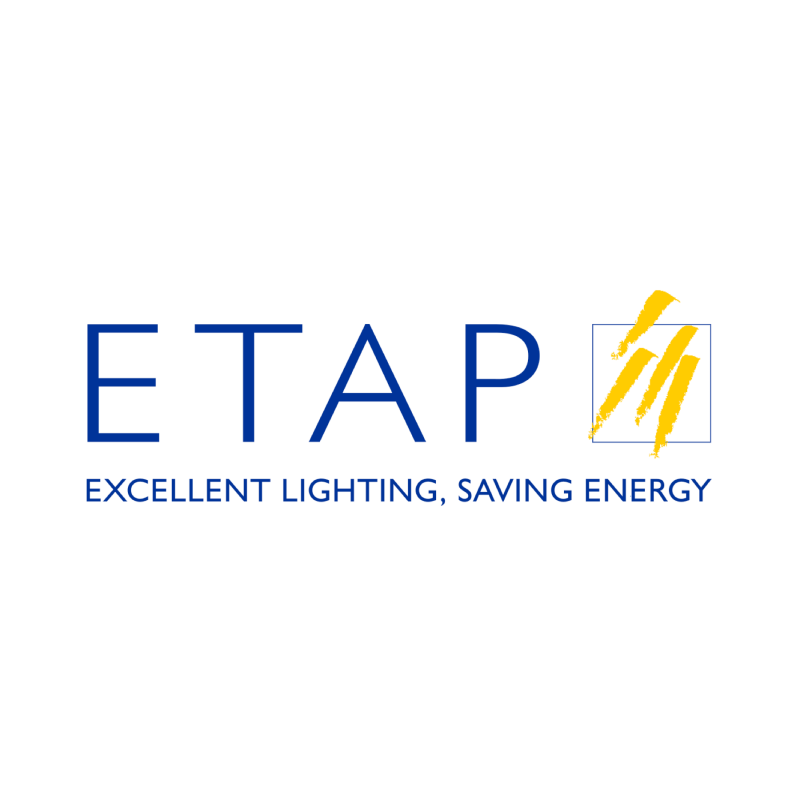